11 photos
Parlee Cycles was born out of boat building. For many years, founder Bob Parlee crafted high-performance race boats out of carbon fiber and, on the side, shaped wooden sailboats. During this time, Bob Parlee was also racing bikes, but as a rider he was never satisfied with the quality, performance and fit of off-the-shelf bikes. The boat builder figured he could do bicycles better, so in 2001, he took his attention to detail, knowledge of carbon fiber and love of bikes and created Parlee Cycles, a small carbon bike manufacturer making frames entirely by hand — from fork to dropout. And to understand why cyclists will spend $7,000+ for a Parlee frame, I visited Bob Parlee in his studio.
Situated next to the railroad tracks of the Newburyport/Rockport “T” line and down the street from the Bowl-O-Mat bowling alley in Beverly, Massachusetts, you wouldn’t think twice driving past Parlee Cycles. Its exterior is modest, constructed from whitewashed cinder blocks, and the only thing that gives away that this is a bike shop is a branded trailer parked out front. This humble facility, by appearance, stands in contrast to some multimillion-dollar research and development facilities of larger brands. But despite its size, Parlee is making bikes that surpass the quality of the bigger companies.
“Some of the little details are lost when people talk about weight and stiffness, but the little details, for us, make the bike.”
Each and every custom frame that comes out of the Parlee shop is made entirely by hand, in house — including the tubes. In my research, no other brand in the US can make that same claim. Most custom carbon bike makers use pre-made tubes from other companies, like Edge Composites. Not Parlee. Parlee uses a proprietary process (which they keep very close to the chest) in which the carbon tubes have pressure applied to them from the inside out. This gives them the flexibility to create literally any shape and length tube imaginable, which translates to custom bikes that are comfortable enough to ride all day while still offering high performance.
To create the tubes and to assist in the layup of the frame, Parlee uses what are called pre-preg sheets of carbon fiber, or carbon fiber weaves that already have resin embedded in the fibers. To shape them, you “just turn on the heat,” Bob Parlee explained. Of course, it’s a bit more complicated than that. Each custom frame starts with measurements, then moves to tube construction, assembling the tubes to create a rough frame, grinding and sanding, and finally painting — which Parlee also does in house.
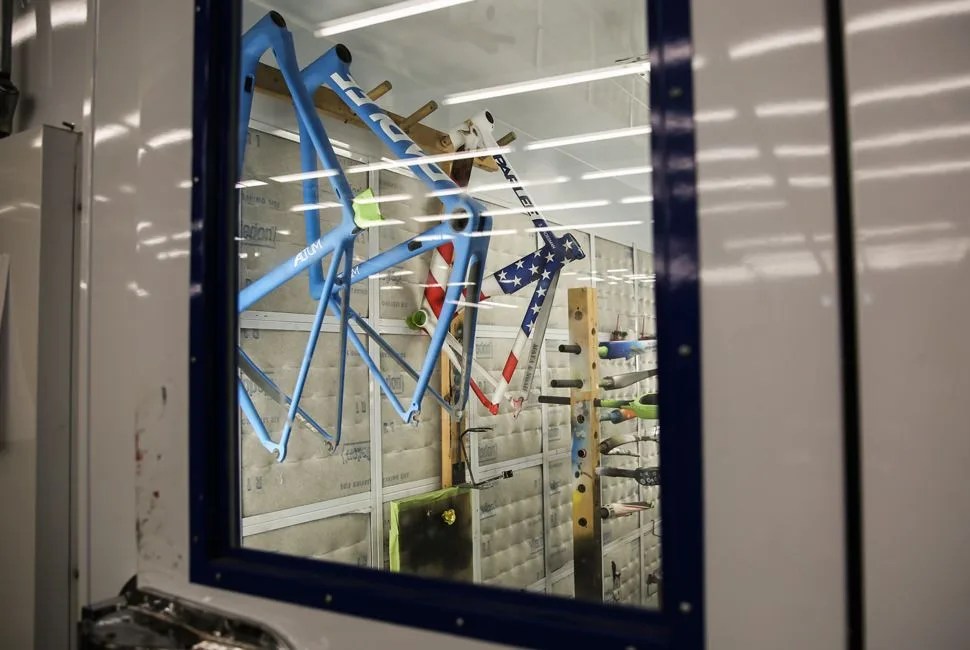